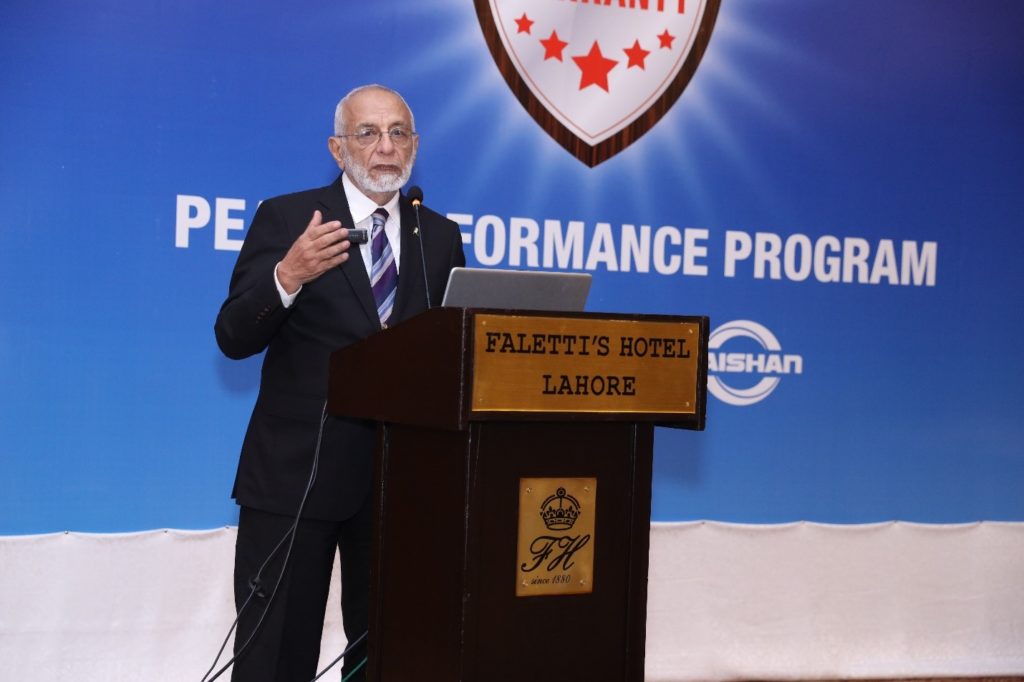
Millions of miles of fabric are produced every year using compressed air driven spinning machines and air jet looms. Ensuring a quality stream of compressed air is essential in minimizing fabric staining and
production loss. With increasing demand, textile manufacturers must select an efficient and cost-effective solution that provides a quick return on investment.
Producing beautiful fabrics, with the most sophisticated colors and patterns is an art. Fashion designers entrust their creations only to weavers or spinners who are able to deliver the highest quality.
That’s why textile producers consciously choose 100% oil-free compressed air. Because you know quality and productivity do matter.
ISO 8573-1
100% Oil-Free Air Allows
Textile Manufacturers To
Maintain High-Quality
Standards.
Air-Jet Weaving
Compressed air is blown through fine nozzles to transport the weft. Oil in the air blocks the nozzles, leading to production stoppages and costly nozzle replacements. Fabric staining will also result, causing product rejections.
Exhaust air from the nozzles blows over the air-jet weaving machines. Any oil present deposits on the reeds. It attracts dust and fibers causing the reeds to stick together and break. Resulting production losses and reed replacements are very expensive.
Air-Jet Spinning
Cotton is spun into yarn using compressed air through fine nozzles. Oil in compressed air will lead to nozzle clogging. It will also stain the yarn, which is in direct contact with the compressed air. Expensive nozzle replacements, production losses and product rejections will result.
Pneumatic Transport
The production of man-made raw materials, for use in textiles, also uses compressed air. One of the applications is the pneumatic transport of PVC, PTA or DMT chips. Oil contamination can cause substandard products besides being a fire hazard. Oil may also damage controls and instrumentation components, resulting in breakdowns.
Texturizing
In this process, yarn is intermingled using a jet of air through a nozzle. Blockage due to oil will cause uneven intermingling and destroy the yarn. Staining of the yarn will also result.
In many applications, such as yarn texturizing or textile weaving high volumes of compressed air comes in direct contact with the manufactured fabrics. To help maintain high-quality standards, CompAir compressors provide ISO 8573-1 Class 0 oil-free air
and show minimal variation at extreme flow demands.
In addition to properly selected equipment ,delivery quality can be continuously monitored through instruments indicating quantity of oil, dust and moisture in air.
Conclusion Oil in Compressed Air will lead to quality problems and steps must be taken in selection of air compressors as well as maintenance
of filtration equipment for delivery of 100% oil free air. Addition of these instruments to air transmission lines can lead to control over air quality.