KRSP2 SERIES COMPRESSORS
Low cost of ownership throughout life cycle
Compressed air is often referred to as the ‘fourth utility’ and is critical to most manufacturing operations. Facility performance depends upon compressor
reliability and efficiency.
Power consumption is a significant cost throughout the life cycle of a compressor. Therefore, it is important to consider the life cycle cost of a compressed air system when evaluating productivity improvements. LX series advanced energy saving features reduce operation costs significantly
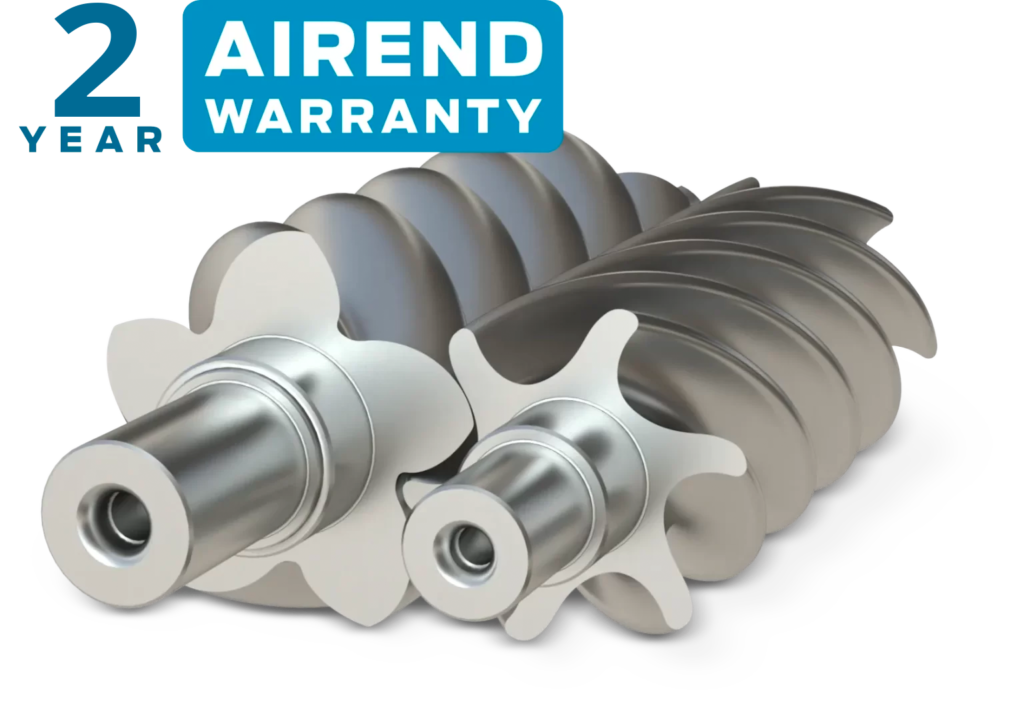
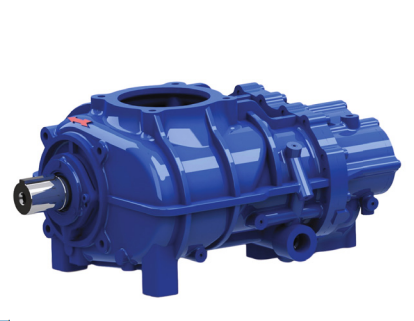
Continued development has increased efficiency by more than 20% over earlier models
- Two-Stage air end design for high flow rate and low power consumption
- Direct coupled through gears motor and air end operate at slow speed
- Low part load energy consumption
- Steady system pressure lowers system pressure fluxuation and overall air demand
- Slow speed male rotors maximize performance and increase reliability
- Decreased energy consumption reduces carbon footprint and delivers cost savings
- 5 / 6 rotor profile creates optimal performance while reducing energy consumption
- 2 in 1 intake valve design (with check valve) for increased efficiency
- Direct flow inlet valve provides reliable capacity control
- Triplex SKF bearings for durability and reliability
- Very tight tolerances provide maximum efficiency
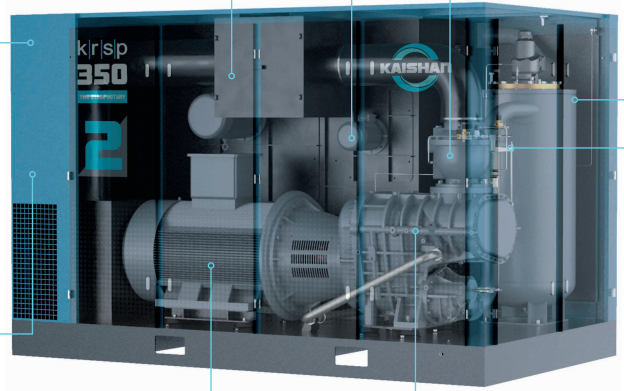
SINGLE PASS OIL & AFTER COOLERS
Long Life / Easily Accessible
- Minimize thermal stress
- Cooler running temperatures / correct running temperature @ 122F° (50°C) ambient capable
- Low oil carryover increases bearing life
- Low cooling air velocity reduces dust build up
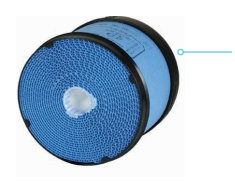
‘ULTRAWEB’ AIR INTAKE FILTERS
Increased Filtration Efficiency
- Full airflow, low restriction, nanofiber technology
- Deep bed media ensures excellent dust capture
- Increased free air delivery for further savings in energy and running costs
CENTRIFUGAL COOLING FANS
Increased Cooling Efficiency
• Higher static pressure allows for heat recovery ducting
• Even air flow across the cooler face.
• VSD cooling fan (150 HP and above) provides energy savings as cooling airflow is reduced during periods of light load or low temperatures
• Cooling air bypasses main compressor compartment resulting in minimal internal dust build up
LAMINAR FLOW INLET VALVE
Minimum Pressure Drop / Increased Output
• Laminar flow inlet valve results in lower pressure drop through the intake, increasing output and saving energy
3-STAGE TANGENTIAL OIL SEPARATION
Lower Pressure Drop / Lower Absorbed Power
• Excellent oil mechanical pre-separation/ reduced direct oil impingement onto separator element
• Lower dust contact resulting in lower pressure drop / longer element life / lower energy consumption
• Residual oil carryover limited to 3 ppm
DIGITAL CONTROL PANEL
Monitors & Controls Key Compressor Functions
• Protects compressor in the event of a fault
• Provides service required alert
• Sequencing of up to 16 compressors
• External monitoring via RS 485 interface
• WYE Delta starter is standard on all models
• MODBUS capability
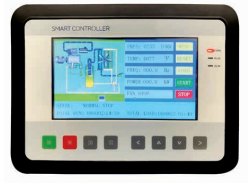
SAFETY AND THE ENVIRONMENT
Reduced OSHA Risk and Injury
• The entire Kaishan range of compressors includes full safety features such as guarded rotating components and shrouded electrical components
INDUSTRIAL GRADE ELECTRICAL COMPONENTS
Increased Reliability / Lower Servicing Cost
• Outstanding reliability
• Excellent component life
• Worldwide support
• Standard electrical parts available locally
HIGH-EFFICIENCY ELECTRIC MOTORS
Long Operating Life / Lower Power Use
• Kaishan uses high efficiency motors, which comply with all international standards
• Motors are standard TEFC to IP 54 protection from dust and moisture
• Class F insulation
• Cooling air bypasses main compressor compartment resulting in lower component operating temperatures and longer life
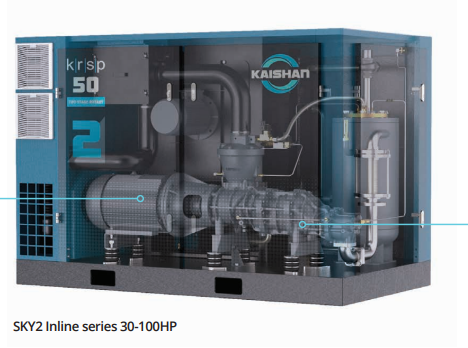
316 STAINLESS STEEL CONTROL TUBING
Long Tubing Life / Reduced Downtime
• Increased reliability due to corrosion free material
• Material such as nylon, copper or mild steel will fail in time causing downtime
316 STAINLESS STEEL CONTROL TUBING
Longer Bearing Life / Quieter Operation
• The “SKY2” series airend uses three discharge bearings on the first stage and four bearings on the second stage
• Longest bearing life in the industry
• Warrantied for a “Lifetime” of use
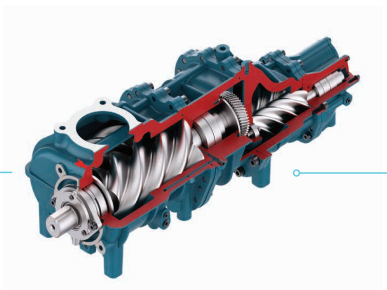
‘SKY’ SERIES AIR END
Maximum Output with Less Energy Usage
• Asymmetric 5 / 6 rotor profile with 100% SKF bearings
• KAPP Grinder rotor technology for tighter clearances and world class efficiency and performance
• Precision machined bell housing to SKY2 Inline series 30-100HP maintain rigid alignment
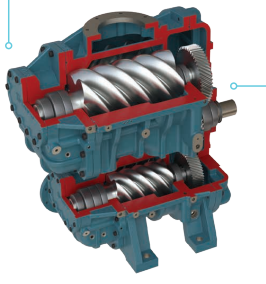